Activated Carbon Screening Equipment
Activated Carbon Screening Equipment
The MH gyratory screener and and MHG side doors access gyratory screener is the suitable activated carbon screening equipment.
As we know, the actived carbon powder is one kind very light material, the vibration model screenwith high frequency do not have good screening result, the strong vibration force will throw the material into the air and had to pass the mesh aperture.
But for our MH model gyratory screener with low frequency and large stroke, it is one proper activated carbon powder screening equipment. For more details, please feel free to contact us
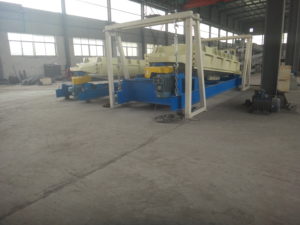
activated carbon screening